Cars are becoming exponentially more complex – and it’s impacting the fleet industry and the insurers who protect them. The situation is likely to worsen, with an estimated 100 new electric vehicle manufacturers entering the market in the next years.
The days of a single body shop having the skills to diagnose, repair, and restore all make and models of vehicles are coming to an end. In a world of ever-increasing car complexity, repairers must specialise to ensure they can deliver the highest quality work at the optimal price point.
Identifying suitable specialist suppliers is a growing challenge for fleet operators and insurers. The solution is Repair Manager that uses data to allocate repairs across your body shop network.
Advanced integrations
Lift the bonnet of a modern car, or slide into the driver's seat, and you'll quickly notice how much vehicles have changed in the last five years. In fact, the integration of technology and the adoption of new materials mean that four wheels, seats, and a steering wheel are often the only standard features.
EU legislation is making driving safer for drivers, passengers, and pedestrians. But, behind the scenes, it's also changing how all vehicles are designed, engineered, manufactured, and maintained.
Across Europe, automotive manufacturers face a dizzying array of legislation dictating the materials that can and should be used in vehicles. Driving the adoption of new materials is a requirement that at least 85% of parts must be able to be reused or recycled.
Traditional materials such as cast iron and steel are rapidly being replaced by lightweight materials, including aluminium, high-strength steel, alloys, polymer composites, and carbon fibre. Lighter cars need less fuel to move the mass, which cuts emissions and costs for drivers. Additionally, new materials are often stronger making vehicles lighter, safer, and more sustainable.
New materials have unique properties and require specialist repairs. Shops must invest in the tools and technologies to work with each type of material. Alongside this, engineers must develop the skills to work with complex materials, understanding the potential and limitations of materials. The increasing complexity of materials and the sheer variety used in vehicle manufacture mean it's not practical for a single shop to service and repair every vehicle type.
As well as influencing the materials used to build cars, EU legislation is changing the technologies inside them One of the most significant shifts is the integration of Advanced Driver Assistance Systems (ADAS) systems within new vehicles. These vehicles systems achieve four things:
- Draw attention to approaching traffic
- Signal road users located in the driver's blind spot
- Assist the driver in directing their attention to relevant information
- Provides prior knowledge of the next traffic situation
ADAS systems aren't optional but must be an integral part of each new vehicle, states EU (Regulation (EU) 2019/2144). As well as ensuring ADAS systems are included in all new vehicles, there is a compelling case for them to be retrofitted to existing cars. ADAS can dramatically cut crashes but will dramatically increase vehicle complexity.
ADAS is covered by several complex standards, including ISO 26262, ISO/SAE 21434, and ASPICE, which provide strictures for manufacturers and repairers. Simply put, vehicles with ADAS systems installed are more complicated and costly to repair.
Introducing new technology at scale is critical to achieving EU plans to reduce emissions by at least 40% by 2030 – and it will change much of what we take for granted. However, advanced materials and driver assistance technologies are the tip of the iceberg. In forthcoming years, the greater adoption of hybrids, electric vehicles, and potentially even hydrogen power will pose more significant challenges for everyone in the automotive industry.
Industry adaptation
The number of car accidents is falling each year, say EU figures. Experts suggest that ADAS systems could help avoid up to 62% of all crashes. Any reduction in casualties is encouraging, but the reality is that no system can stop accidents from occurring, and no materials are impervious to damage. This means that, for the foreseeable future, at least, vehicle repair shops will still be required.
It’s also apparent that the increasing complexity of cars, alternative materials and advanced safety systems will increase repair costs. For example, a recent study shows that the costs for simple repair activities on the front or rear damages can be almost two and a half times more expensive than that with a vehicle without ADAS.
Consider a simple bumper crash. Previously, a body shop could swap the bumper for an OEM replacement, but it's more complex with an ADAS vehicle. The bumper will still need to be replaced alongside a new sensor. Once the physical repairs have been completed, the system will need to be reset and recalibrated to ensure it functions correctly.
Evidently, a body shop will need a much broader range of skills in-house to complete the repair, covering both physical skills and software knowledge. They may need to invest in proprietary equipment for each manufacturer's vehicles, costs which will inevitably pass to consumers. Working with advanced materials can be challenging for even the most experienced mechanics. Alongside technical knowledge of materials, operators will be required to invest in new equipment essential to making such repairs. And the more services you offer, the greater the costs.
In the future, body shops will become transformed into high-tech centres. They will need the latest tools and technologies to enable them to perform repairs – including software to manage systems. Alongside this, they must invest heavily in training and supporting staff to develop the necessary skills to maintain, service, and repair ever more complex vehicles.
Specialisation for survival
The vehicle repair industry is braced for a massive number of new entrants, all with different software, systems, and solutions that will stretch the skills of even the most advanced engineers. In reality, body shops will no longer be able to offer a complete repair service for all vehicles. Specialisation is critical to survival.
Companies can focus investment and attention in several ways, including on a specific brand, drive line, or damage type. It may seem counterintuitive in a time of increasing competition to limit your market, but the complexity means it's only possible for generalists to develop the skills required to repair all types of vehicles safely.
Critical for any body shop (or business) is having the ability to deliver the highest quality service at the optimal price while achieving volume levels. This doesn't mean that all body shops should immediately invest thousands in expensive ADAS systems and fabrication equipment. Instead, the challenge is identifying and exploiting a niche, filling your capacity, and accelerating growth.
Navigating complexity
Specialisation may be central to the survival of suppliers, but the impact of the shift will significantly impact fleet operators and insurers. They can no longer rely on a single solution but must enter the market. They must ensure that the repair centres they choose have the capacity and skills to complete repairs to the agreed standards.
Industry insiders are always searching for better deals but increasing car complexity and specialisation will make it harder to select the best supplier manually. Technology has created this problem, and our Repair Manager platform forms a critical part of the solution.
Repair Manager is part of Openclaims' end-to-end solution that uses data insights to drive better decisions. It offers fleet operators and insurers four key benefits:
- Repair Manager enables users to create business rules that automate the distribution of individual damages to the best-suited body shop.
- These dynamic business rules can be amended or tailored to any situation or scenario. The ability to review and refresh business rules is critical as fleets grow and change.
- Repair Manager incorporates an AI model that interprets the historical performance data of repair networks to identify which body shops are good at repairing specific types of damages. The intelligent machine learning algorithm can process hundreds of variables to select the most suitable repairer for every task.
- These insights in body shop skills combined with certifications and specialisations that you can access in Repair Manager facilitate automated individual matchmaking between damage and repairer according to the business rules. Within the system, users can create contractual agreements and SLAs to simplify the contractual process.
Repair Manager also offers control to contractors. Each body shop can create, manage, and maintain its profile. They can add, edit, or remove skills, providing real-time control and capacity management. The Network Manager module provides operators easy access to their established network of vehicle repairers to facilitate faster repairs at the highest quality. The platform enables some of Europe's largest fleet operators and insurance companies to take control of their repair needs, ensuring cost-efficient repairs for even the most advanced cars and vehicles. The result is lower-cost repairs, happier customers, and higher retention rates.
You May Also Like
These Related Stories
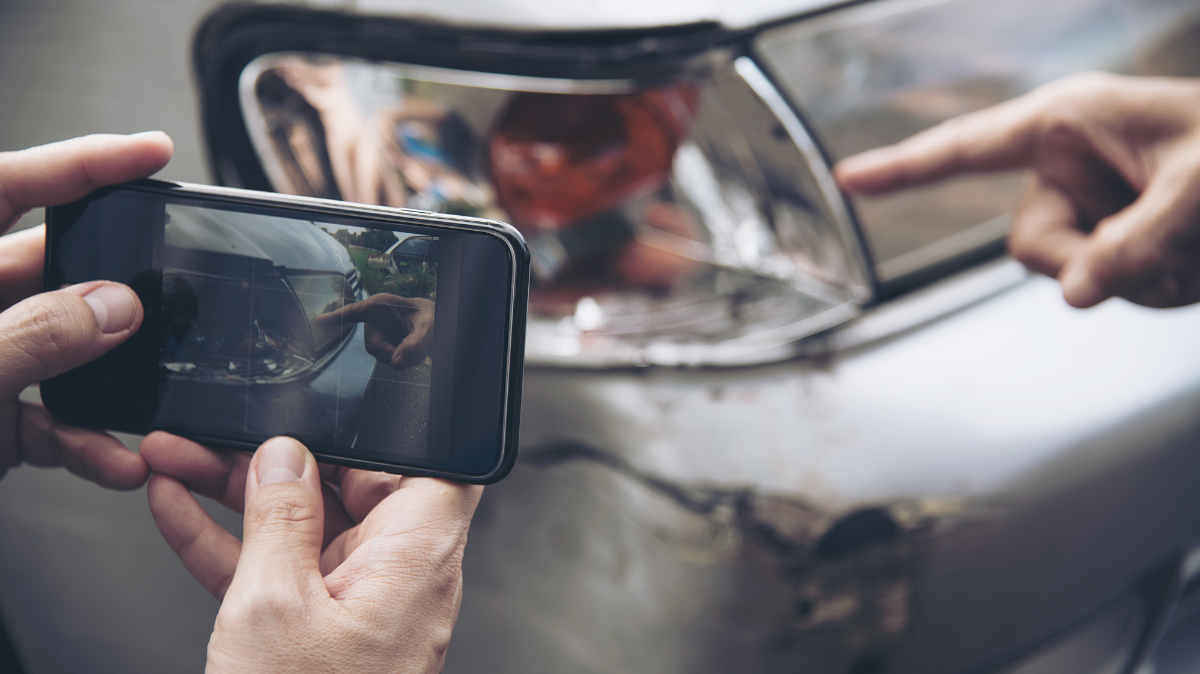
Why a Seamless Claims and Repair Process Is Essential for Customer Retention
.png?width=1920&height=1080&name=How%20leasing%20companies%20can%20use%20data%20to%20improve%20repair%20distribution%20and%20reduce%20costs%20(Website%202025%20image).png)
How leasing companies can use data to improve repair distribution and reduce costs
.png?width=1920&height=1080&name=Hedin%20Customer%20Spotlight%20(Website%202025).png)