Repair managers face increasing challenges in their daily work, largely due to the growing complexity of vehicle repairs. The influx of new vehicle brands, advanced technologies, and innovative materials means that modern cars require highly specialized knowledge to be repaired correctly. However, repair managers often lack insight into the specific capabilities and specializations of their contracted body shops, making it difficult to assign repairs to the right workshop. On top of that, they often don’t have the (software) tools needed to streamline this process, further complicating their job and leading to inefficiencies that drive up costs.
These inefficiencies don’t just affect expenses; they also extend key-to-key times, delaying vehicle returns and frustrating customers. Furthermore, incorrect repair allocations can compromise both safety and sustainability, further increasing the overall cost and complexity of repairs.
To tackle these challenges, a smarter, more efficient way of distributing repairs is needed—one that ensures every vehicle is sent to the right body shop at the right time. This is where the Distribution Engine comes in.
From Damage to Repair: How the Repair Distribution Engine Works
Meet Alex, a BYD driver who just discovered a dent in his car after a minor parking mishap. Frustrated but determined to get it fixed quickly, he turns to the online Body Shop Finder to locate the best repair shop in his area.
Alex starts by answering a few simple questions about the damage—where it is, how severe it looks, and whether it affects any critical vehicle functions. As he submits the details, the Repair Distribution Engine gets to work behind the scenes.
First, the system enriches Alex’s input with additional data—pulling in relevant details about his BYD model, its high-voltage battery system, and any special repair considerations. It also factors in contract or policy data from his insurer or leasing company, ensuring all necessary conditions are met.
Next, the business rule engine kicks in. This engine applies a set of rules that can be fully customized by the insurer or leasing company handling Alex’s claim. These rules could be straightforward—such as limiting body shop options to those within a 20-kilometer radius—or more specific, like requiring the shop to have a High-Voltage Certification or even an official BYD brand certification to guarantee expert handling of electric vehicle components.
To ensure the right match, these rules and requirements are cross-referenced with extensive body shop profiles stored in Network Manager, a powerful database that provides deep insight into each shop’s specializations, certifications, and capabilities.
With this data, the system generates a shortlist of eligible body shops, all fully equipped to handle Alex’s BYD repair. But the selection process doesn’t stop there. The list is then automatically ranked based on a scoring system that the insurer or leasing company can configure. This ensures that not just any shop appears at the top, but the best shop for the job—whether based on location, certification, cost efficiency, or customer satisfaction scores.
Finally, Alex is presented with a ranked list of repair shops. With all the critical factors considered upfront, he simply selects the best option from the list, confident that his BYD will be repaired by specialists who meet both his needs and his insurer’s requirements.
By streamlining what was once a complex and manual process, the Repair Distribution Engine takes the guesswork out of repair assignments—ensuring efficiency, cost control, and peace of mind for both repair managers and drivers.
With the Repair Distribution Engine, repair managers can assign repairs more efficiently, eliminating the inefficiencies that drive up costs. By ensuring that every repair goes to the most suitable body shop, our software significantly reduces repair expenses while also shortening key-to-key times, allowing vehicles to return to the road faster. Additionally, it enables insurers and leasing companies to set up and automate specific contractual agreements, ensuring that policies and preferred networks are followed—without repair managers having to manually oversee every detail. With the right technology in place, repair managers can focus on keeping operations smooth, cost-effective, and hassle-free.
You May Also Like
These Related Stories
%20.png?width=1920&height=1080&name=Feature%20Focus%20Body%20Shop%20Scorecards%20(Website%202025)%20.png)
Feature focus: Body Shop Scorecards
%20.png?width=1920&height=1080&name=Feature%20Focus%20Automatic%20Liability%20Determination%20(Website%202025)%20.png)
Feature focus: Automatic Liability Determination
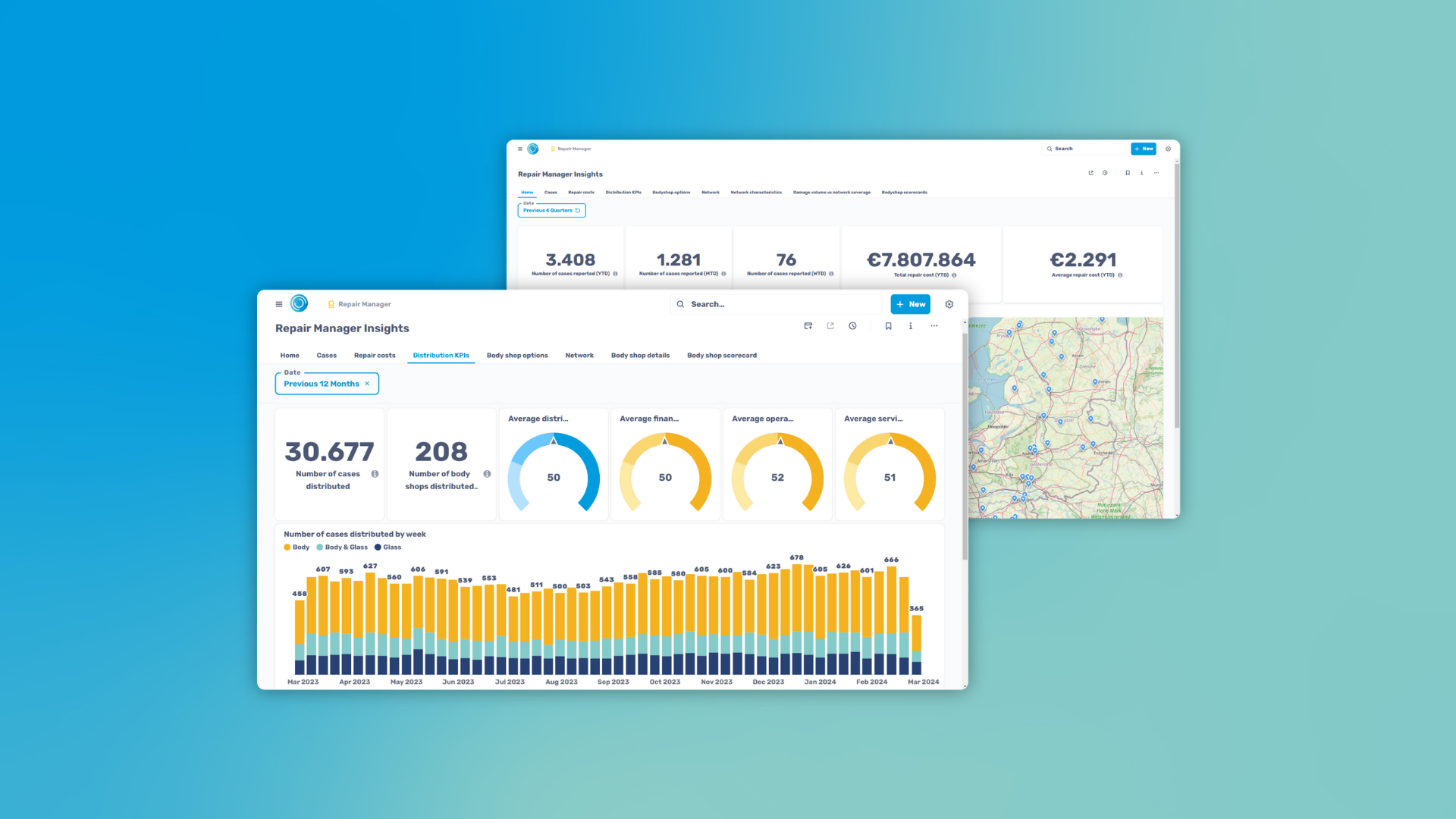